The Future of the Machinery Industry is Digital: Marcel's Highlights from EMO 2023 in Hannover

Marcel, our specialist in Digital Transformation and Industrial Automation at SIROC, recently attended the EMO conference in Hannover, Germany. This event is known for featuring the latest advancements in metalworking technology, such as machinery, tools, and state-of-the-art solutions. It offers a forum for global manufacturers and professionals to come together to exchange knowledge, establish relationships, and form business partnerships.
While the metalworking industry has celebrated numerous successes in the past, Dr.-Ing. Heinz-Jürgen Prokop, President of CECIMO, emphasized in his keynote that relying on past achievements is no longer viable. To remain competitive, it is essential to leverage the newest technological advancements.
While the exhibition had many impressive exhibitors, a stroll around it clearly reveals that several manufacturers have yet to embrace the digital age.
If they fail to act quickly, their competitors will outpace them by taking advantage of Artificial Intelligence, Machine Learning, and Data Engineering, and combining it all into a modern and slick User Interface and overall User Experience.
Innovations at EMO 2023
But instead of just talking vision, let's take a look at some bright examples of industrial machinery companies that have caught our attention:
DMG Mori
Few displays at EMO 2023 could rival the grandeur of DMG Mori. Taking over an entire hall with their dedicated "DMG Mori City," the company provided a captivating glimpse into the future of machining.
Their commitment to sustainable practices is evident in the introduction of the 'green mode' in their machines. This innovative feature promises up to 30% energy savings by leveraging consumption-optimized components. For instance, DMG Mori has incorporated LED lighting or utilized the potential of recovering braking energy.
The mill-turn centers by DMG Mori are a testament to the brilliance of integrated technology. Traditionally, a workpiece might need to be set up on separate machines for turning, milling, grinding, etc. Each setup takes time and increases the chances of errors due to the misalignment of the part. In a mill-turn center, a workpiece is set up once and can undergo multiple processes
Perhaps the highlight of their exhibit was the unveiling of the industry's very first end-to-end digital twin of a machine tool. A digital twin is a virtual representation of a physical object, process, or system. It bridges the physical and digital realms by collecting real-world data from the physical entity and using this data to create, simulate, and analyze its digital counterpart. With the aid of advanced analytics, Machine Learning, and AI, the digital twin can help optimize performance, predict failures, and even suggest maintenance tasks.
DMG Mori's showcase at EMO 2023 reaffirmed their position at the forefront of innovation, setting a benchmark for others to aspire to.
Walc, Inc.
DMG Mori even went further and launched their own subsidiary (Walc, Inc.) in the spirit of an independent, but well funded startup with the aim to develop solutions using AI, IoT and Cloud Computing.
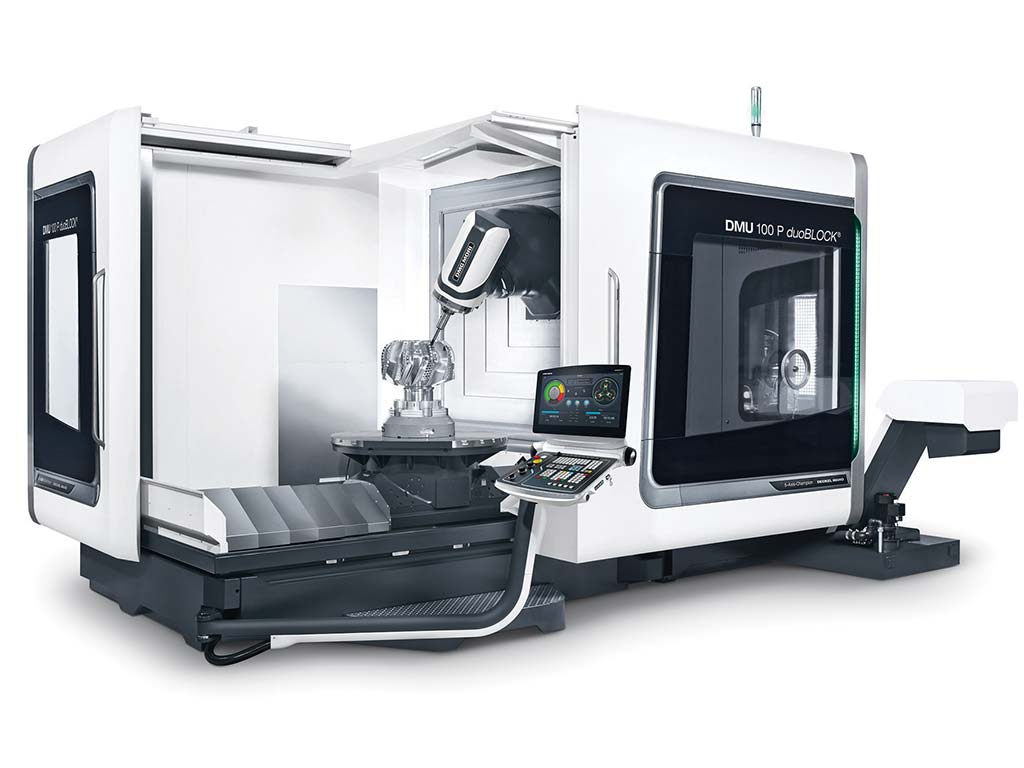
Their key product, WALC CARE, enables the automation of machine maintenance. With predictive maintenance and optimized repairs, it achieves early fault detection and cost reduction. Real-time monitoring and AI diagnostics enable maximizing productivity and strong business promotion.
This is similar to the custom Anomaly Detection solutions offered by SIROC AI.
CloudNC
CloudNC's primary innovation involves leveraging Artificial Intelligence (AI) and advanced computation to optimize the CNC machining process. Traditional CNC programming can be time-consuming and requires expert knowledge. CloudNC aims to automate much of this process, turning 3D designs into machined parts more efficiently and rapidly than conventional methods. Their software algorithmically determines the most efficient way to produce a part, aiming to reduce waste, costs, and production time.
Schunk iTENDO²
The iTENDO² toolholder by SCHUNK detects irregularities through its digital process monitoring capabilities. Specifically, it's positioned "closest-to-the-part" in the metal-cutting process, which makes it ideal for signal acquisition. Once connected, the iTENDO² can immediately identify irregularities by monitoring vibrations and vibration peaks during the machining process. The data it gathers can then be visualized in real time, providing users with immediate feedback. This allows for process transparency, with the goal of improving tool service life, optimizing cutting data, and enhancing overall surface quality.
Fraunhofer: Bio-Inspired Manufacturing
The Fraunhofer Institute for Production Technology (IPT) has initiated the research project "BioManu", which aims to revolutionize sustainable circular economics by integrating biology with technology.
Focusing on enhancing the thermal performance of machine tools, the project harnesses bionic structures and principles. Notably, the research delves into utilizing biobased insulation materials derived from fungal networks, known as mycelium, and integrating them into insulations around a machine tool.
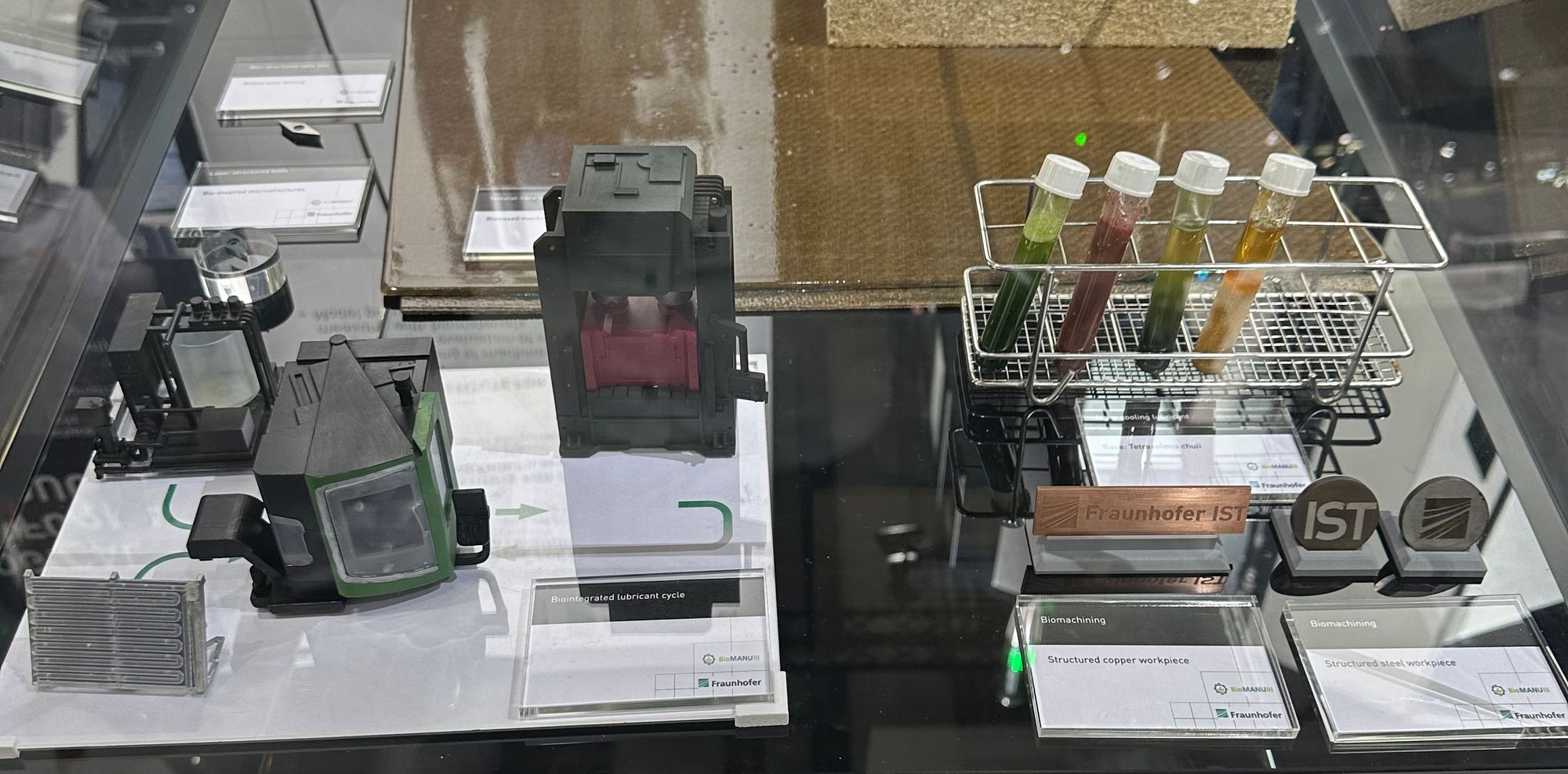
Conclusion: The Future of the Machinery Industry is Digital and Automated
After an exciting week at the EMO trade fair, it's quite clear that the future of the Machinery Industry is Digital, Green and Automated. Here are some general trends that we have noticed:
Smart Factories
Automation of Manufacturing: Traditionally, automation in manufacturing has involved using machinery and technology to perform specific tasks that were once done manually. This has allowed for faster production, more consistent product quality, and reduced manual labor. However, the processes are largely deterministic, meaning the machinery does exactly what it's programmed to do without much adaptability or real-time decision-making based on the current environment or unexpected events.
Autonomy of Manufacturing (Smart Factory): Autonomy introduces a higher level of intelligence and adaptability into the manufacturing process. A smart factory, equipped with advanced data analytics, artificial intelligence, and interconnected devices (often referred to as the Internet of Things or IoT), can make decisions on its own. For example, it can adapt to changes in the production line in real-time, optimize operations based on current conditions, predict maintenance needs, and even reconfigure itself for new products or designs. The focus shifts from simply automating tasks to creating a responsive, adaptable, and self-optimizing system.
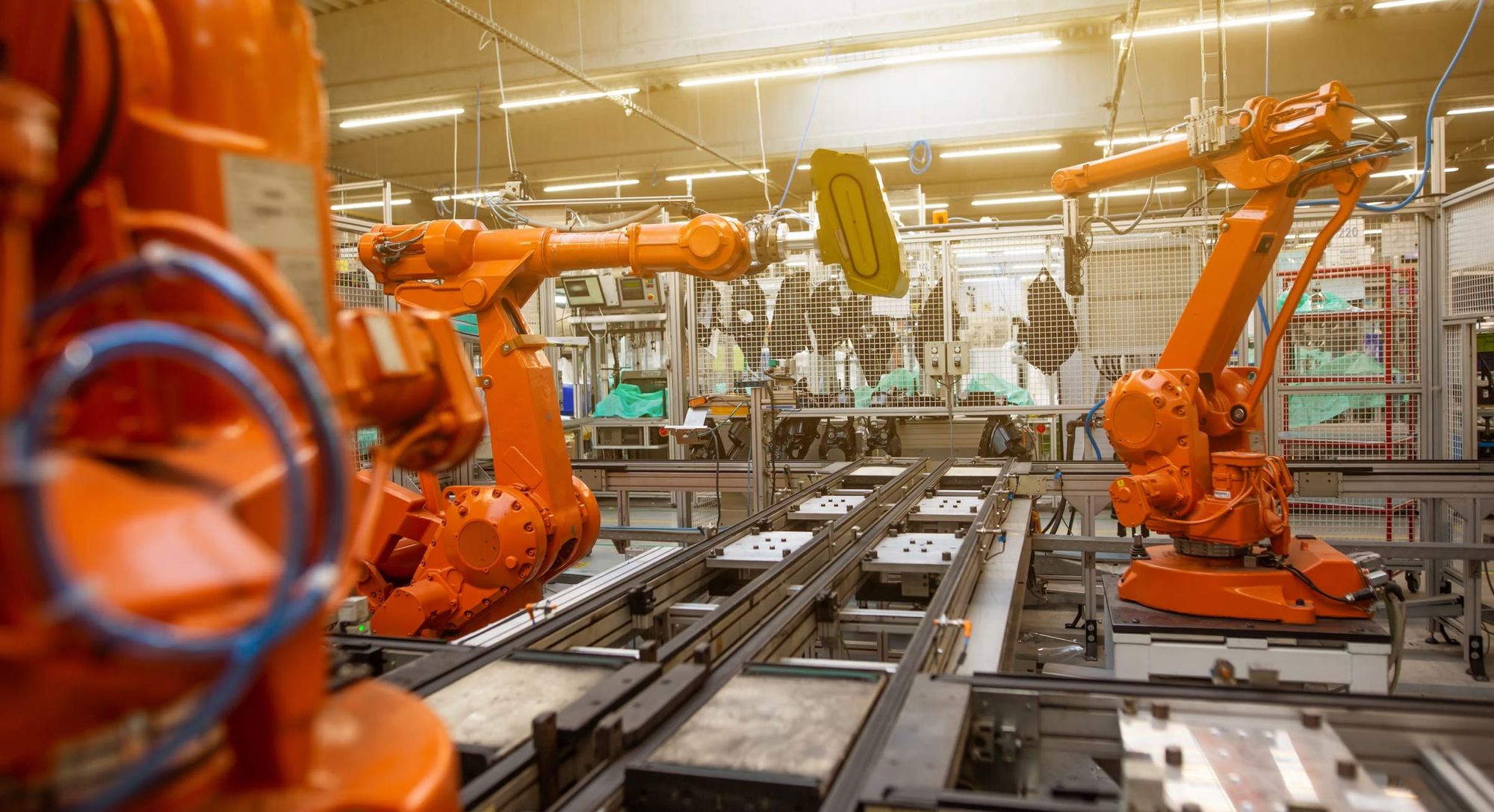
The Fully Autonomous Supply Chain
Driven by a combination of Artificial Intelligence (AI), the Internet of Things (IoT), and Advanced Data Analytics, these self-regulating systems can process vast amounts of data in real-time. This enables them to make proactive decisions—from rerouting shipments based on real-time traffic conditions to adjusting manufacturing schedules based on sudden spikes in demand or material shortages.
Furthermore, the integration of blockchain technology ensures traceability and transparency across the entire chain, instilling confidence and trust in both businesses and consumers. Drones and autonomous vehicles, too, play a pivotal role, ensuring goods are transported seamlessly and efficiently from one point to another.
Process Integration: The Future of Efficient Machining
Companies like DMG MORI are pioneering this shift, championing the integration of diverse processes into singular, multifaceted machines. Imagine the benefits of having one machining center adept at turning, milling, grinding, and even intricate measurement functions. This isn't just a matter of conserving floor space; it's about elevating productivity. Instead of having several machines operating below their capacity, process integration ensures high utilization of a single, comprehensive machine.
Process integration is more than a mere trend. It's a transformative approach set to redefine the very core of manufacturing. As technology continues to evolve, integrating multiple processes into single machines represents not just significant efficiency gains, but a more sustainable future for the manufacturing world at large.
Harnessing the Power of Data: Predictive Maintenance and Anomaly Detection with Machine Learning
Unexpected glitches and downtimes can throw off entire production schedules, incurring costs and compromising deliverables. But what if we could foresee these glitches and act even before they manifest? This is the promise of Predictive Maintenance and Anomaly Detection.
At its core, Predictive Maintenance isn't just about anticipating when a machine might need attention. It's about understanding the myriad signals a machine emits, sifting through them to spot the early warning signs of potential issues. And while this sounds like looking for a needle in a haystack, with the power of data analytics and machine learning, it becomes not only possible but incredibly precise.
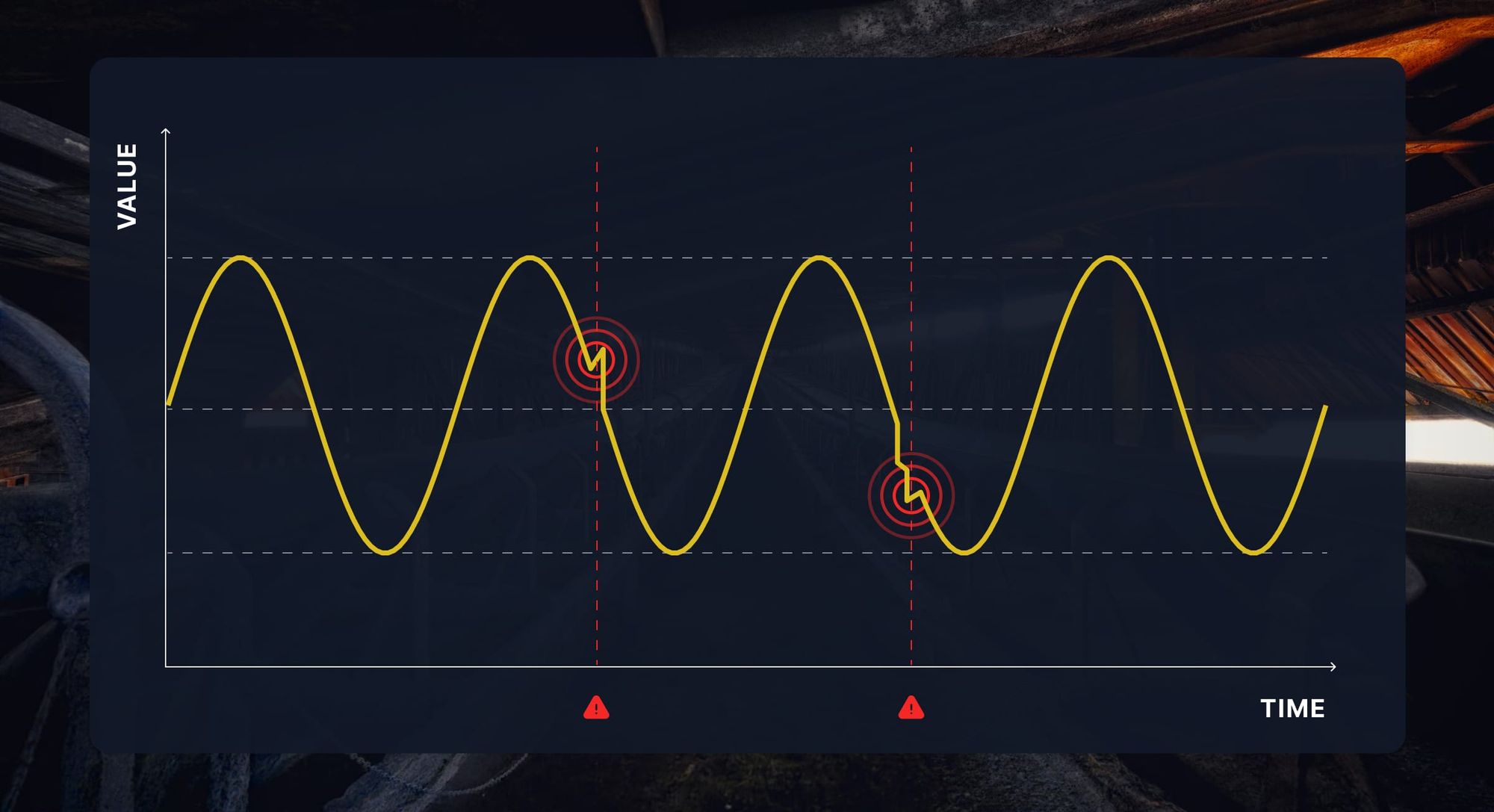
Anomaly Detection takes this a step further. Every machine has its rhythm and pattern of operation, and any deviation from this 'norm' can be a sign of an impending problem. By training Machine Learning models on vast datasets detailing normal machine operations, these algorithms become adept at picking out even the slightest aberrations. Such deviations, which might be imperceptible to human operators or traditional monitoring systems, become glaringly obvious under the scrutiny of advanced anomaly detection techniques.
If you're interested in this topic, we recommend our blog post on how we implemented Anomaly Detection at a cement plant:
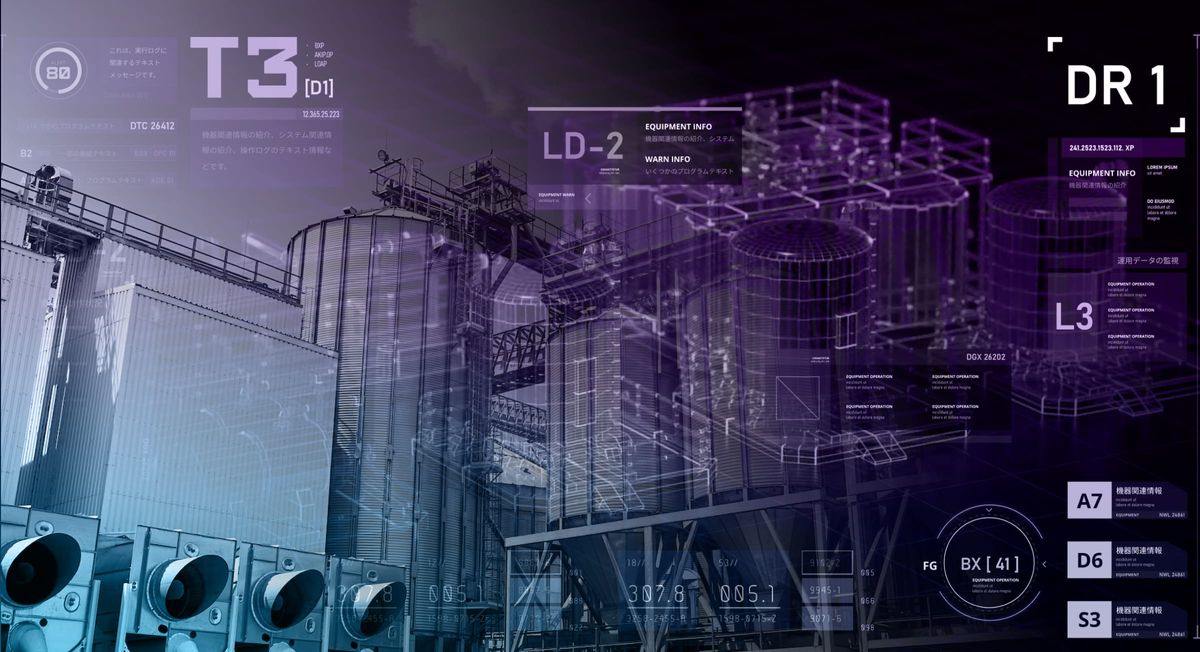
About SIROC
We hope our innovation report from EMO 2023 sparked your interest in how Data Engineering and Machine Learning can be applied to the Machinery Industry to achieve new heights of scalability and profitability.
If you need assistance or advice with data analytics, data engineering, or integrating ML/DL models into your business, don't hesitate to reach out to us at SIROC. We specialize in developing custom AI solutions tailored to your needs, such as forecasting models, recommender and decision maker models, as well as anomaly detection models.
Not only do we have an extensive collection of pre-trained in-house models, but we also collaborate with industry-leading partners such as OpenAI and Aflorithmic to deliver cutting-edge solutions to optimize and automate your business. Find out more about our products and solutions on our website.
This post contains images provided by Unsplash.