From Reacting to Problems to Preventing Them With Machine Learning
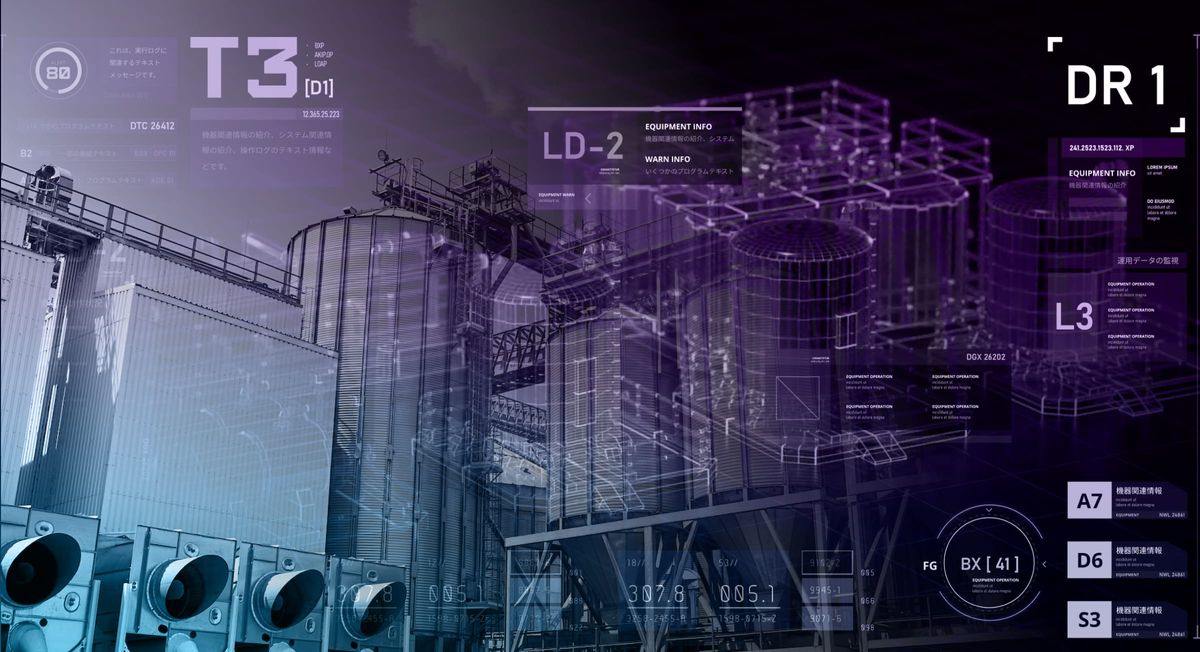
HMI, or Human Machine Interface, is the bridging technology that allows humans to interact and communicate with machines. Typically, you can find these systems housed in control rooms, but they are also located right next to the machines they monitor.
Traditionally, setting up an HMI system requires a hands-on approach. For every piece of data to be monitored, you must manually connect each input to its corresponding output. Deciding on how the data is displayed—whether it's a simple bulb, a numerical reading, a semaphore, or even a gauge—is also part of the process.
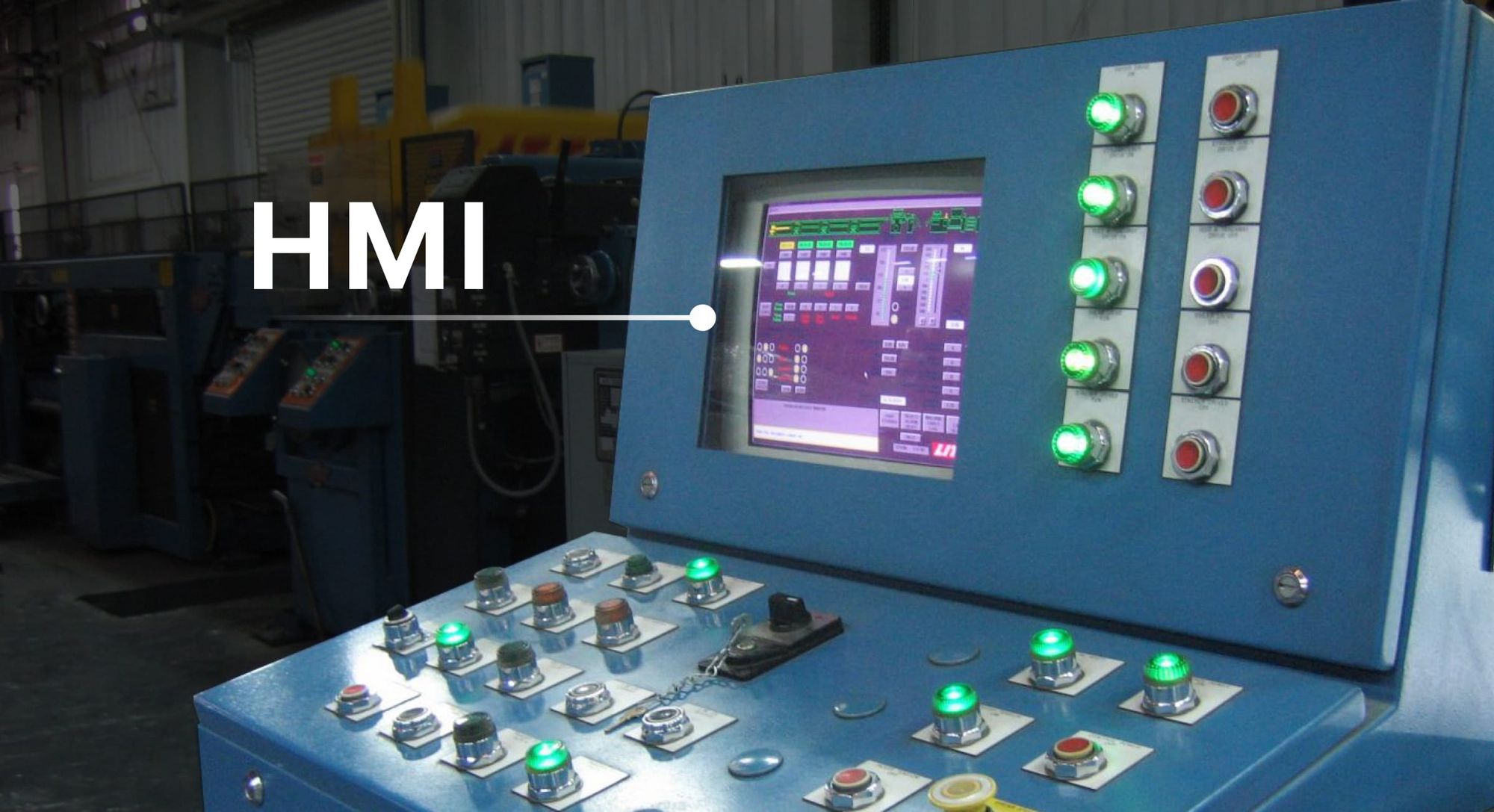
Moreover, while HMI systems can be configured to set off alarms—like turning a bulb red and triggering a siren if certain thresholds are breached—they have a limited scope. If there's a requirement for more intelligent system monitoring, the usual recourse is to acquire specialized software or hardware. But that's not only costly but also a lengthy process.
Our Innovation
Our team at SIROC has pioneered together with our partner companies, a next-generation HMI platform, replacing the old and clunky desktop software from the nineties.
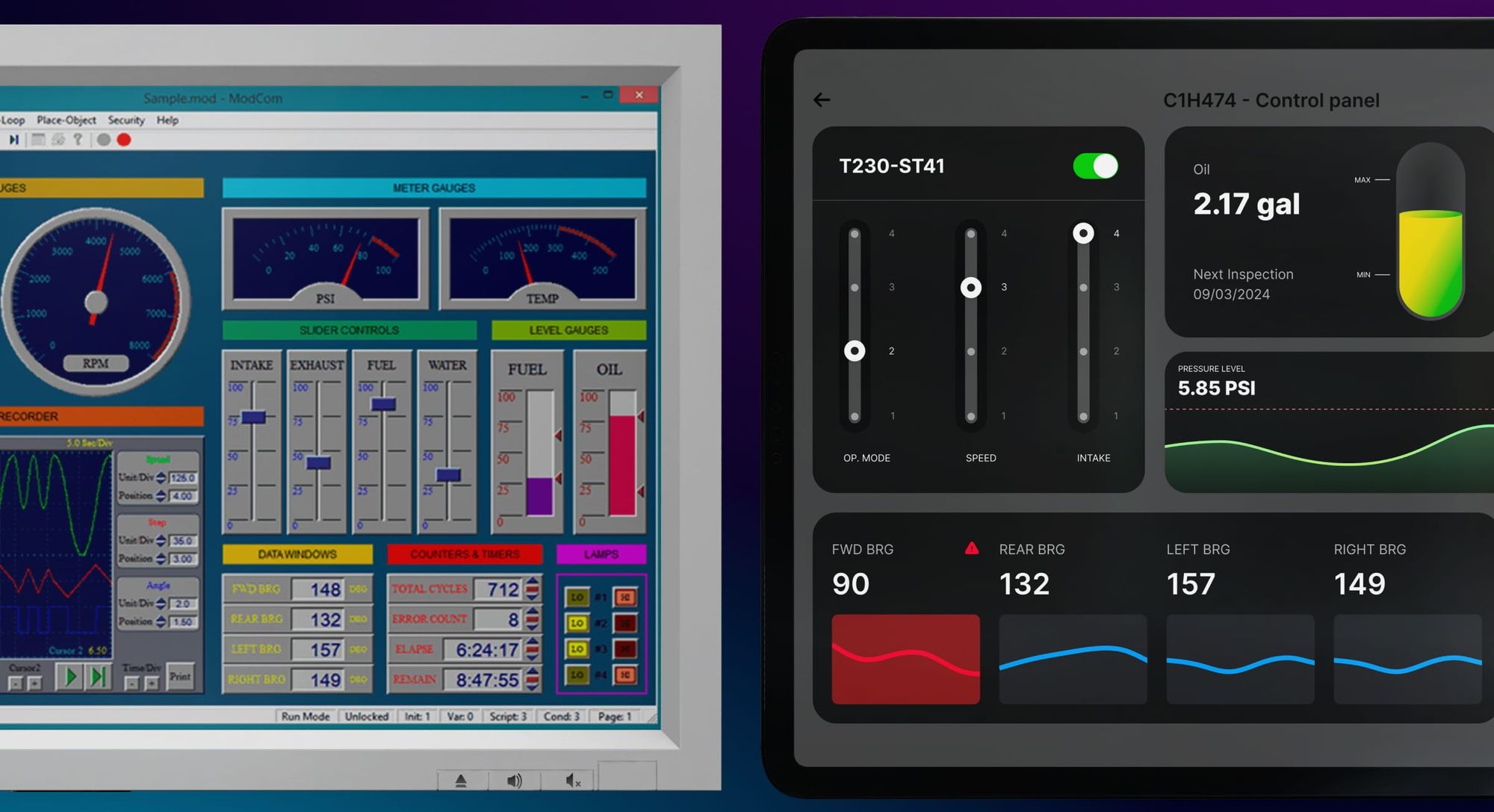
This new technology provides a suite of features that streamlines the experience through an integrated solution combined with an easy-to-use modern interface:
HMI Editor: Designing and developing HMI interfaces is no longer a complex task. The process is intuitive: simply drag and drop visual items or other objects onto pages to create a fully customized user interface.
HMI Cloud: Infrastructure management is crucial, especially when dealing with vast amounts of data and assets. The HMI Cloud provides a managed storage solution for projects and associated assets, such as custom images. All these can be effortlessly uploaded to the HMI Cloud, ensuring a central repository for all essential elements.
HMI Compatibility: Bridging the gap between various machinery brands is a challenge that many face in the industry. Our HMI system adeptly overcomes this by ensuring compatibility with PLCs (Programmable Logic Controllers) across major brands, be it American, European, or Japanese. This extensive compatibility is facilitated by highly efficient native communication drivers, ensuring smooth operations irrespective of the PLC brand in use.
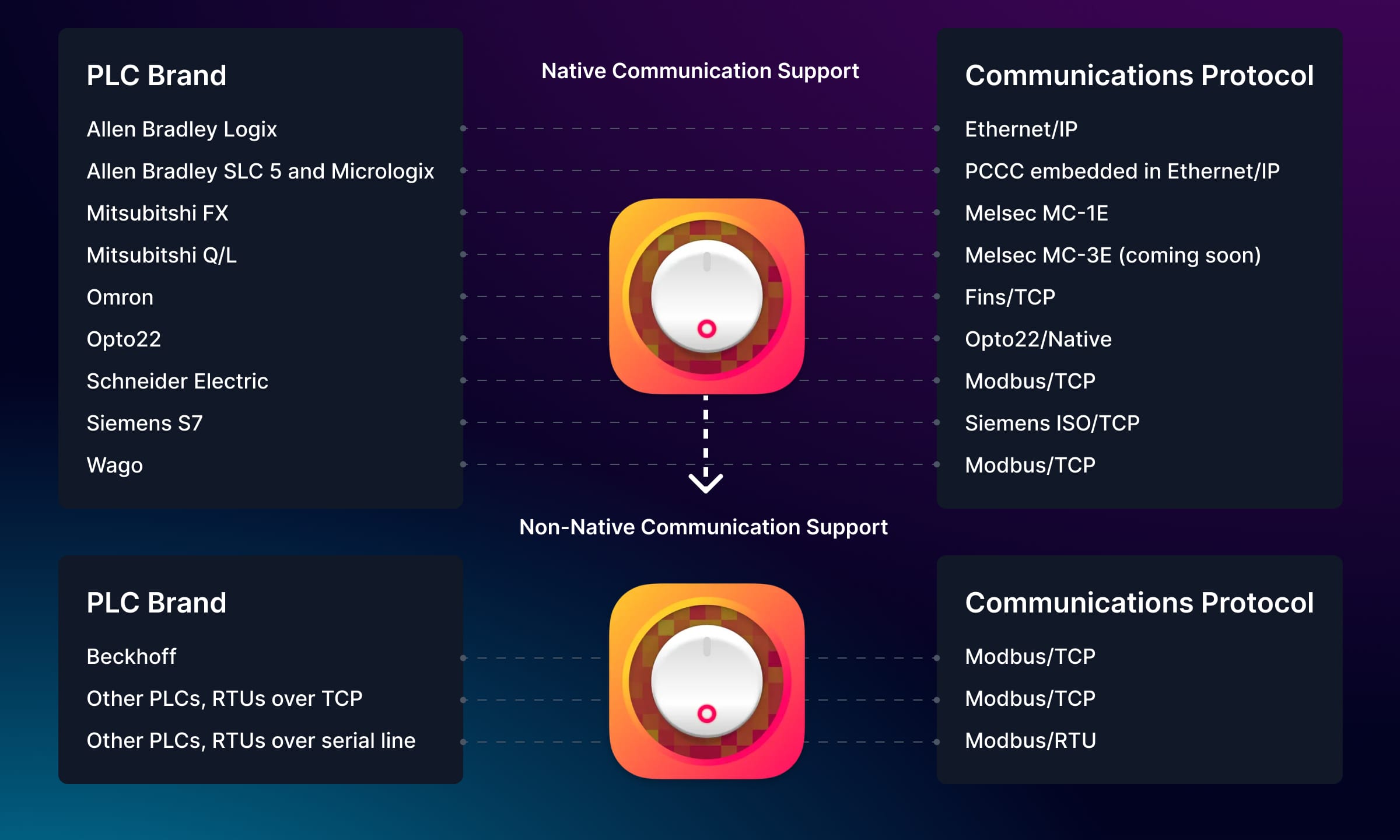
Data-Driven Decisions: The Power of Data Engineering
One of the fundamental aspects of the next-generation HMI system is the robust data engineering capabilities that come with it. This means data flows without hiccups, paving the way for deeper insights and real-time decision making.
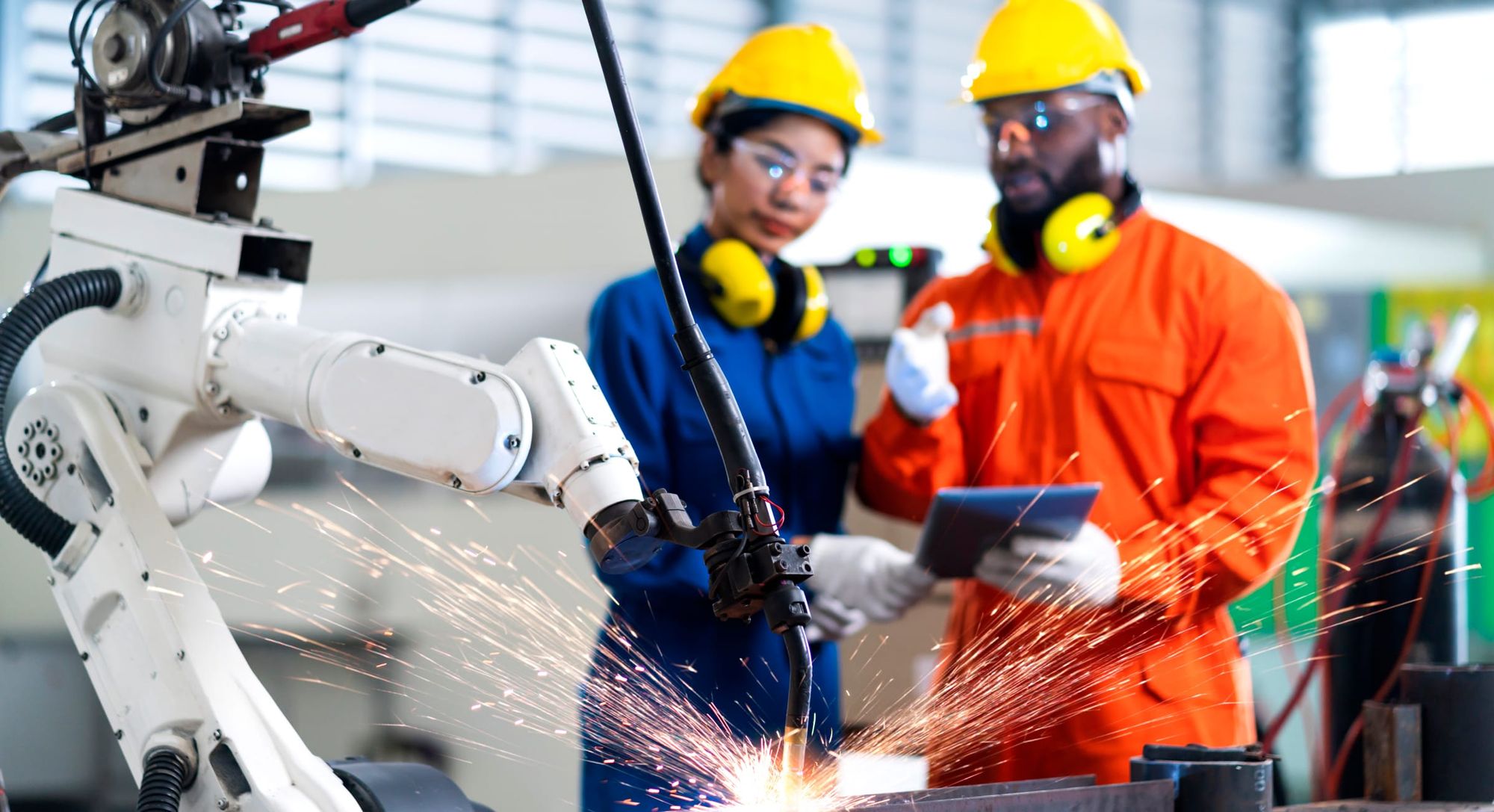
The real benefit of the refined data pipeline is that it not only streamlines the flow of data, but also provides the basis for building advanced Machine Learning (ML) models. These models can be tailored to optimize various factory processes, making the entire system more efficient and responsive.
By relying on real, concrete data rather than guesswork or "gut feelings," companies can address specific challenges and answer pressing business questions with a level of precision never before possible.
One such application is monitoring power consumption. With our system in place, factories can pinpoint the exact moments when power consumption peaks. This knowledge allows for timely intervention, resulting in energy savings, optimized operations, and reduced overhead costs.
An Experiment: Using AI to Detect Anomalies
But we didn't stop there. In an experiment, we integrated Machine Learning models into the platform to detect anomalies in data streams, capable of not only detecting erratic machine behavior, but also predicting potential malfunctions.
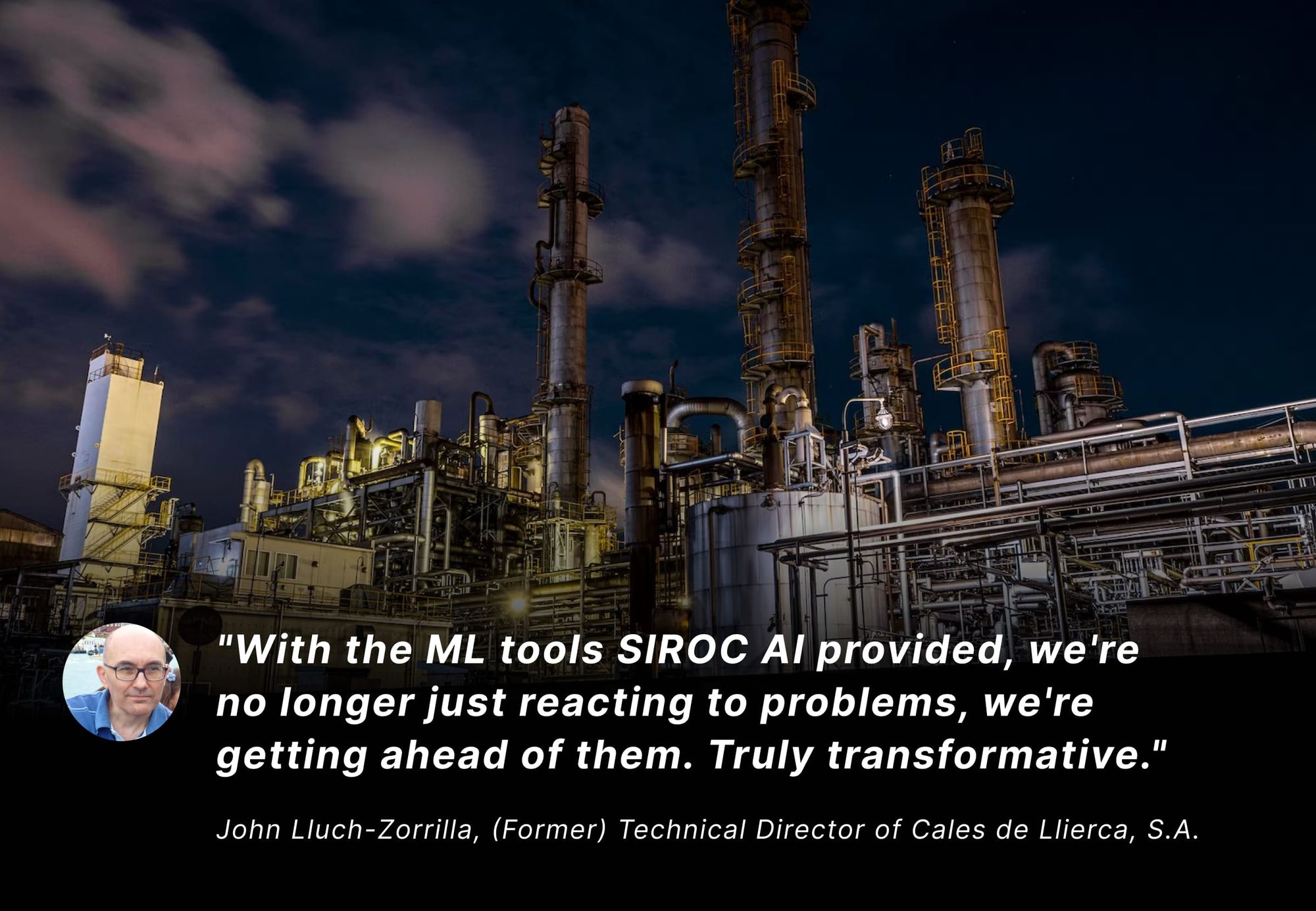
To give you an idea of how transformative this is, consider the case of one of our test deployments at a cement plant. At this plant, conveyor belts are vital but expensive pieces of equipment responsible for transporting rocks. Any malfunction here can bring the entire production line to a halt.
Previously, this plant relied on a traditional HMI system where screens displayed various metrics related to the conveyor belts, such as energy consumption, speed, RPM, and more. While there were alarms set up to warn of abnormal readings, they typically went off when damage was imminent or had already occurred.
However, with our integrated anomaly detection system, the scenario changed. By assimilating all available data points, the anomaly detection system began to differentiate between 'normal' and 'abnormal'. Interestingly, it sent notifications when the belts were under excessive stress - even when the traditional alarms were silent. This led to automated corrective actions, such as speed reduction, preventing potential damage.
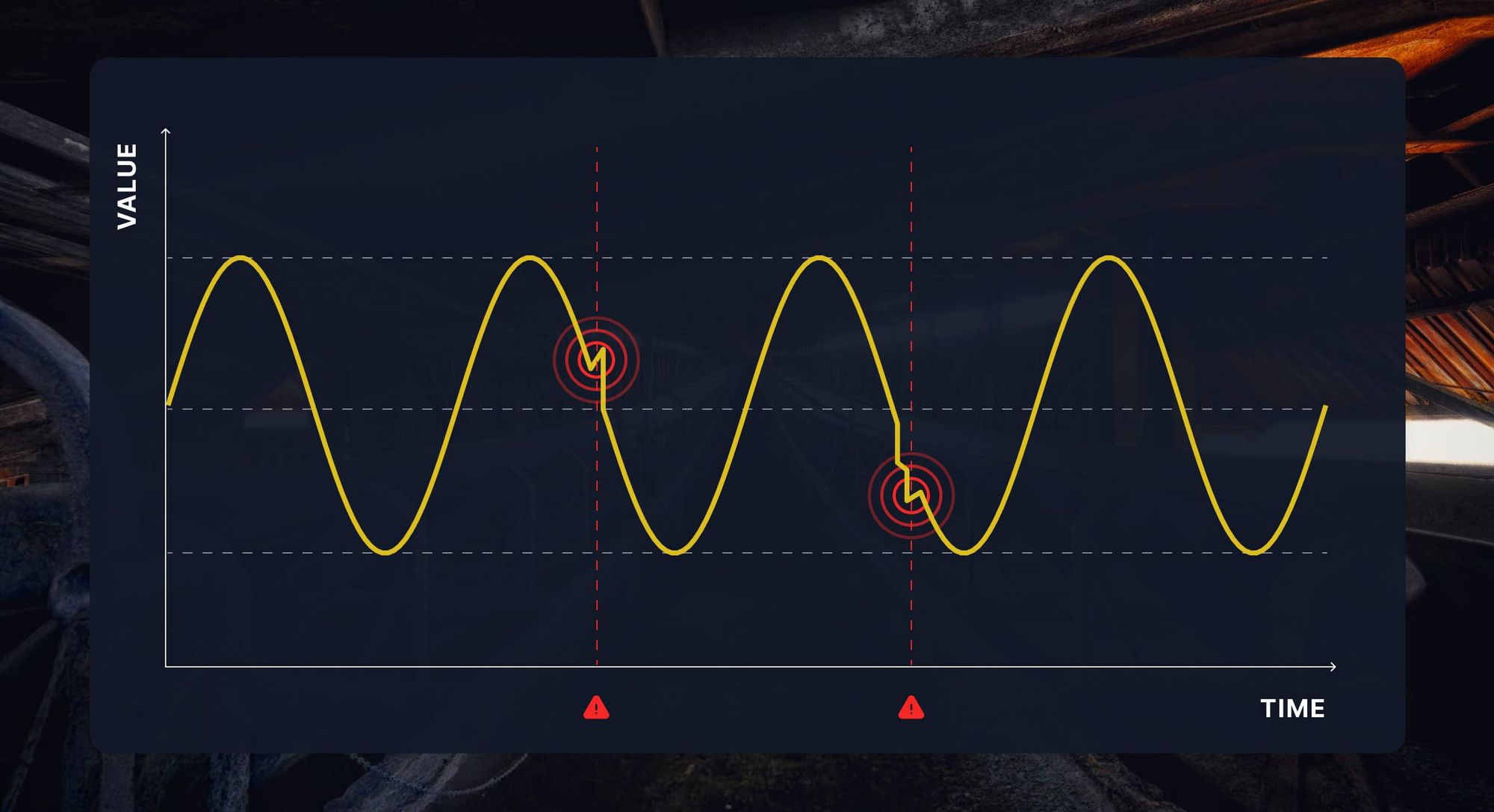
The Benefits are Clear
Proactive Management: Instead of reacting to damages, users can now pre-emptively tackle issues, thereby evading expensive equipment repairs and replacements.
No Unpleasant Surprises: With early detection systems in place, the challenges of unforeseen equipment failures and their consequent downtimes are things of the past.
Efficiency and Profitability: Early detection means scheduled maintenance, leading to maximized productivity, enhanced planning, reduced stress, and, consequently, augmented revenue.
The future of machinery monitoring and maintenance is here. With SIROC's groundbreaking technologies, industries can transition from a manual, reactive approach to a smart, proactive one.
About SIROC
We hope this case study has sparked your interest in how Data Engineering and Machine Learning can be applied to any business to achieve new heights of scalability and profitability.
If you need assistance or advice with data analytics, data engineering, or integrating ML/DL models into your business, don't hesitate to reach out to us at SIROC. We specialize in developing custom AI solutions tailored to your needs, such as forecasting models, recommender and decision maker models, as well as anomaly detection models.
Not only do we have an extensive collection of pre-trained in-house models, but we also collaborate with industry-leading partners such as OpenAI and Aflorithmic to deliver cutting-edge solutions to optimize and automate your business. Find out more about our products and solutions on our website.
Images provided by Freepik.